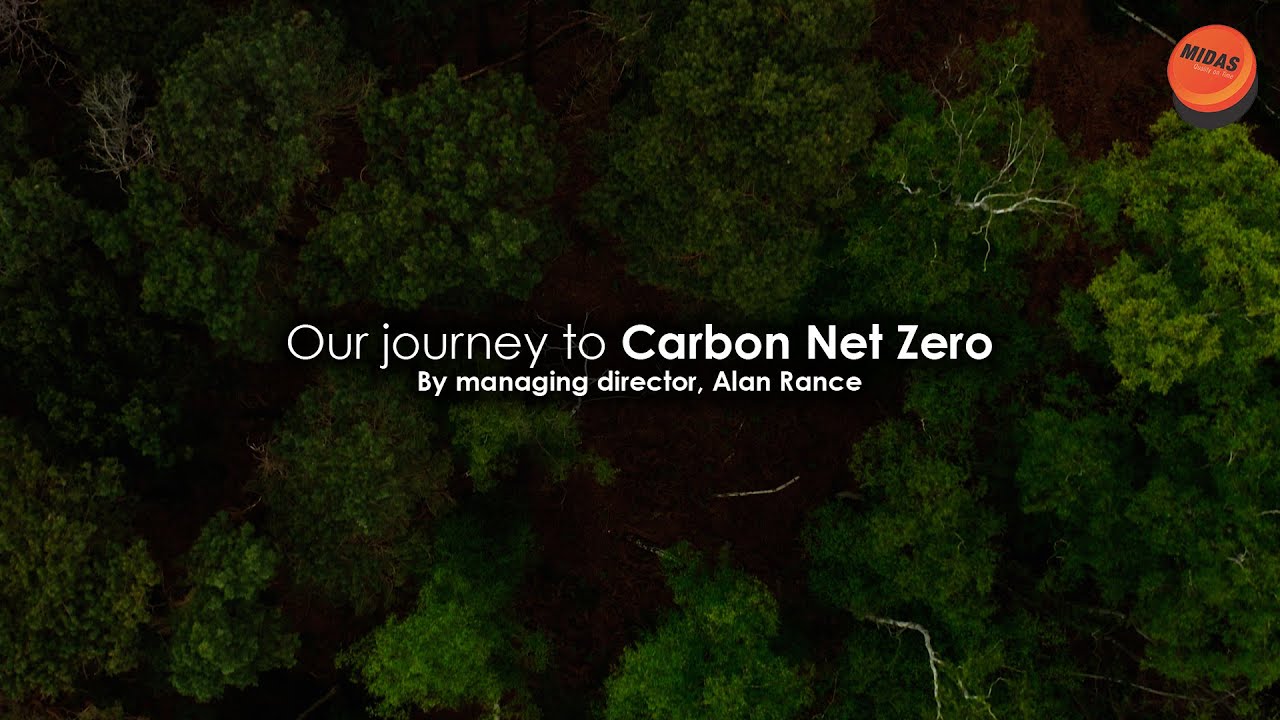
www.midaspattern.co.uk/green-initiative
From 1st January 2021 all Midas products, including our PU mouldings, MRIM & FASTrim tooling, foundry pattern equipment, and engineering models will be delivered completely carbon neutral. In addition to our carbon-neutral manufacturing status, certified by the Carbon Trust, we have also committed to fully mitigate the embodied Carbon within all our products and are therefore ‘Carbon Net-Zero’.
Our Carbon neutral status, embodied Carbon mitigation plan, and our tree planting arrangement with The Forest of Marston Vale, is fully auditable and we would welcome any questions or interest from our customers or local businesses who would like our support in their own carbon reduction plan.
The Environment
Midas is a responsible plastics manufacturer. We take climate change very seriously and believe in the science behind the climate emergency. In order to play our part in reducing Greenhouse Gas (GHG) emissions, we developed the #MidasGreenInitiative to drive change within our manufacturing process and communicate the progress made in reducing our carbon footprint.
Having been ‘process carbon neutral’ since July 2020, we have continued to reduce our waste and energy consumption and strived to improve in all areas of sustainability. By investing in energy-efficient equipment, using renewable energy sources, and investing in 650 photovoltaic panels to create our own Solar Farm, we have continued to make significant progress.
What is the Midas Green Initiative?
The Midas Green Initiative is the name we give our Carbon reduction journey and documents our commitment to an environmentally friendly, Zero-Carbon economy. An economy that supports the fundamental principle of sustainability.
We believe manufacturing doesn’t have to cost the earth and we are proof that by reducing waste, switching suppliers, investing in green innovation and green resources, it is possible to reduce your impact on the planet, achieve carbon neutrality, trade ethically, and responsibly whilst underpinning profitability.
We want to inspire YOU to do the same – Please follow and support #MidasGreenInitiative
The Process
The polyurethane used to make our mouldings is a lightweight structural material that uses very little energy to convert. No temperature control is required in the tooling and mouldings are produced at room temperature. We have no high energy-consuming injection moulding machines or presses as we manually handle our tooling, we pour liquid polyurethane resin at atmospheric pressure which then cures at room temperature.
During the RIM moulding manufacturing process, no chlorofluorocarbons (CFC’s) are produced and the polyurethane is completely inert when cured meaning it will not degrade or leach poisons into the environment. All parts are cast to size ensuring optimum process efficiency with minimal waste thus avoiding the need for additional energy-consuming post-machining.
The Benefits
Our finished RIM mouldings are used in life-enhancing applications from Medical Devices to Solar Panels and EV Charging Stations. They are used positively every day and have a lifespan in excess of 50 years – in simple terms, they are as far from ‘single-use plastics’ as any plastic product can be. When you need a precision moulding, weighing up to 30Kg, potentially measuring in excess of 3 meters, that is robust and has a beautiful finish AND only takes a few watts of energy to make, you know that Midas’ unique polyurethane RIM moulding process is a responsible choice for Green conscious buyers.
Repair, Re-purpose, and Re-use
Using our PU moulding process ensures the maximum return on your investment, it also guarantees quality and longevity, but there are occasions when our mouldings can get worn or damaged, for instance in the field or during assembly. A major environmental benefit of using Midas Polyurethane RIM mouldings is that parts can be returned to us at any time for refurbishment, repair, modification, repainting, rebranding, or simply new graphics, thereby giving you the option to repair and reuse your parts countless times. This aspect of our process ensures you can responsibly recycle your mouldings multiple times thereby reducing downstream waste and of course inevitably saving money. You can read more about how we repair and recycle your RIM mouldings here.
End of Life
When the time comes to recycle your mouldings, the polyurethane used at Midas can be ground down into an inert bulk filler that is used in the construction and composites industry, it will remain inert and environmentally safe for generations to come. If you wish you can return your unwanted mouldings to Midas once they reach their end of life to ensure that they are recycled responsibly or alternatively, if you prefer, you can take guidance from your local recycling specialists.
source